laser automation
Company Background
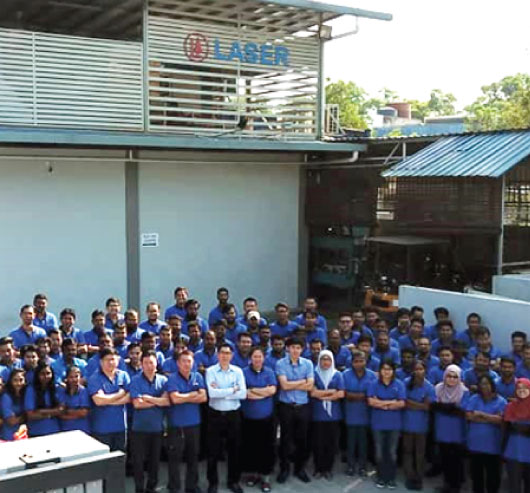
Laser Automation Engineering begun its manufacturing business on April 01, 1992. The company has experienced phenomenal growth since inception and made enormous strides forward by achieving its mission. This has positioned the company to be future-ready in the face of challenges over the next decade. In 1997, Laser Automation Engineering Works experienced a significant change as it evolved into Laser Automation Engineering Sdn. Bhd.
Smartlink Engineering existing facilities are allocated for High Mix & Low Volume and Medium Volume order mode.
Low-cost producer
Accurate quality control
Smart solution manufacturer
Exact delivery time
Reliable service provider
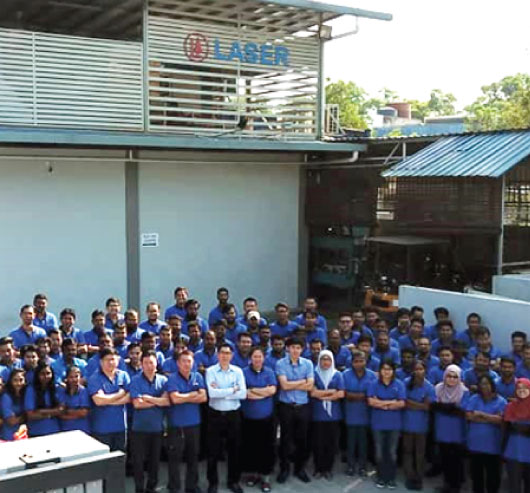
Our mission is to lead the service-providing space for all engineering solutions. We take pride in offering fast, reliable, quality-centered services and workmanship.
0
+
Years experience in High Mix Low
Volume manufacturing
Volume manufacturing
0
Experts in engineering design to
product manufacturing
product manufacturing
0
+
Projects completed in
the last 30+ years
the last 30+ years
OUR PRODUCTS
We have our own Machining and Tooling capabilities and facilities for fabrication of special parts, and to fabricate Jigs and Fixtures. The Company also provides customized machining for customers. We utilize the latest CNC equipment to handle prototype, pre-production, production runs and can develop high tolerance precision parts, jigs and fixtures that require precise manufacturing techniques using high quality components and materials. We offer a one-stop solution for production of precision-engineered systems and sub-modules assemblies and high precision parts and components.
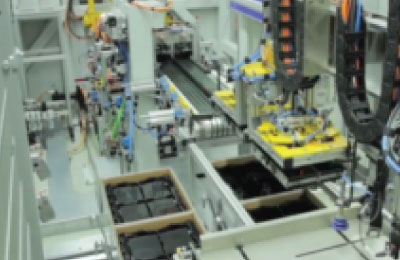
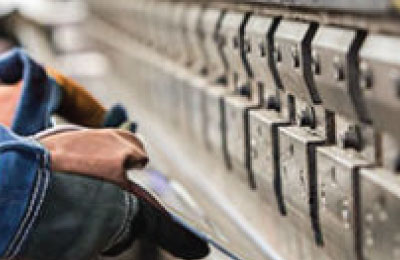
Sub Module Assembly
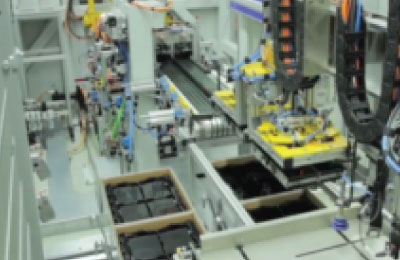
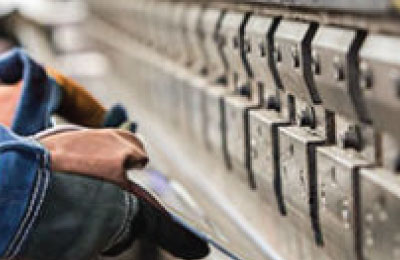
Automation Machinery
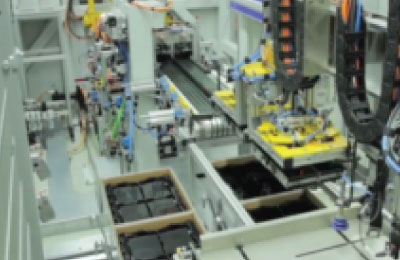
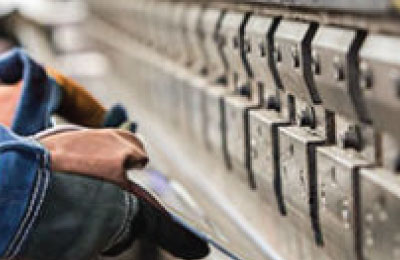
Engineering Plastic
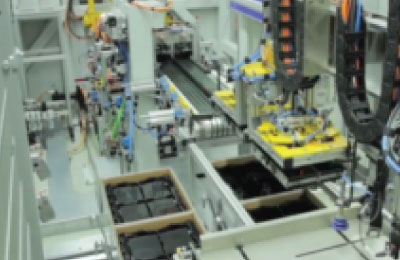
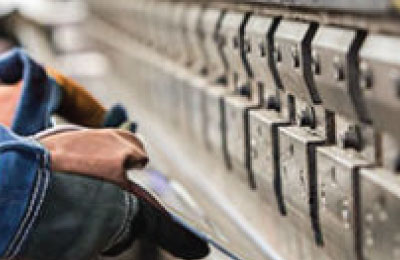
Precision CNC Machining
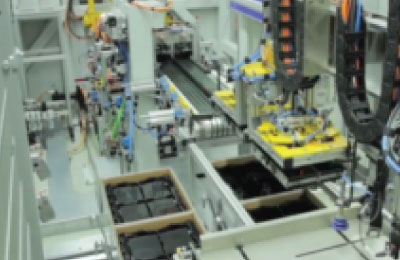
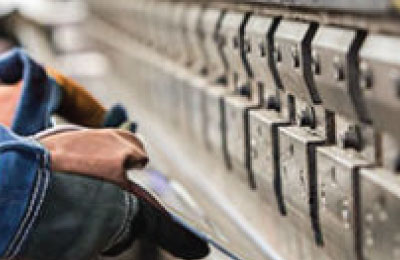
Precision Tools & Dies
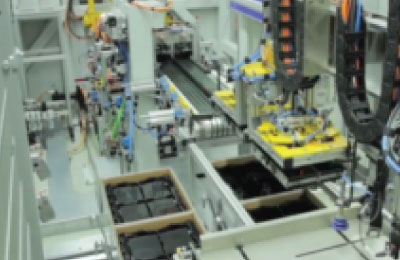
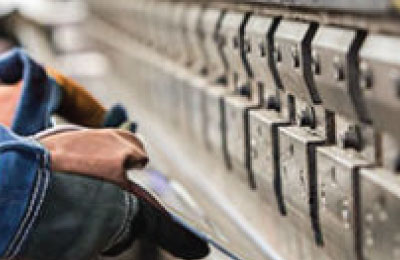
Jigs & Fixtures
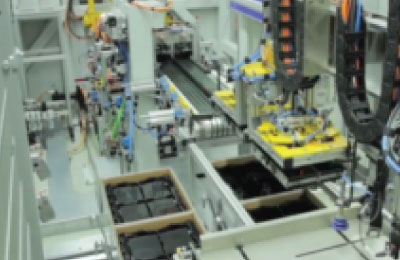
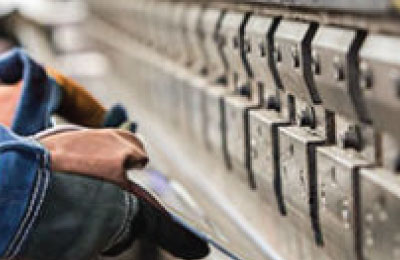
CNC EDM & Wire Cut
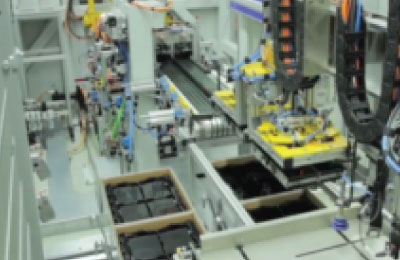
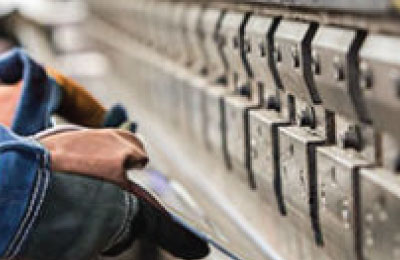
Bending & Welding
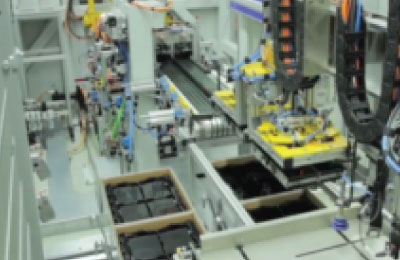
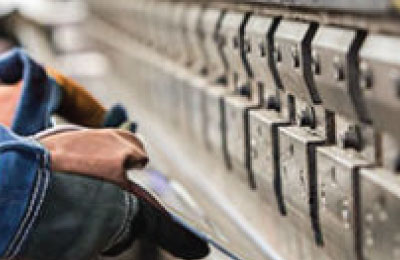
Aluminum Casting & Cast Alloy Parts
OUR SOLUTIONS
Our expertise allows for us to meet the increasing demands of timely service before, during and after a sale. We continuously reassess our services to strive for excellence and support capabilities – revising them when the need arises to remain competitive and foster new business partnerships.
Heat treatment process
- Normalizing & tempering, press tempering
- Vacuum hardening
- Carburizing & annealing
- Induction hardening & flame hardening
- Plasma nitriding & sulfur nitriding
- Tenifer-QPQ
- Sub-zero treatment – 140°C ~ 180°C
Surface treatment process
- Zinc plating – Black, white & blue, rainbow, etc.
- Blackening (black oxide)
- Nickel chrome
- Parkerizing
- Hard chrome / black chrome
- Anodizing-colorless / colored / hard, etc.
- Electroless nickel / Teflon coating
PVD coating process
- TIN (Titanium nitride)
- TICN (Titanium carbonitride)
- CRN (Chromium nitride)
- TIALN (Titanium aluminium nitride)
OUR CLIENTELE
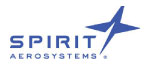
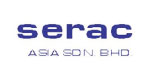
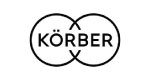
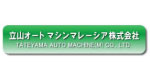
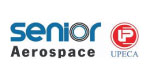
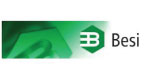
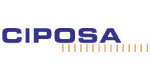
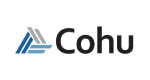
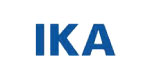
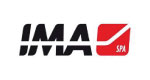
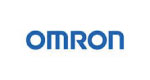
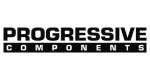
KICKSTART YOUR NEXT PROJECT WITH US
Talk to an Expert & Get a Quotation Now